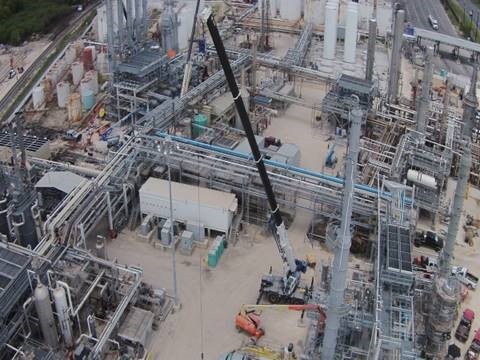
Minimum Cost/Minimum Interruption
Our client desired a specific increase in crude feed rate. The project goal was to provide the increased throughput at minimum cost and with minimum interruption to operations.
Designing the Solution
Polaris engineers performed field test runs to positively determine the capabilities and limits of the existing process equipment. Once this information was developed, Polaris engineers created a new processing scheme using as much of the original unit as possible. The new scheme repurposed a few pieces of equipment, recommissioned some existing equipment and added a pre-flash tower with associated equipment.
Value Added Results
By understanding the performance capabilities of the existing equipment, Polaris engineers were able to offer an innovative solution which reduced the capital required to reach the client’s goal of a specific feed rate. Working closely with the client, Polaris installed the pre-flash tower and associated equipment while the original unit continued to operate. This minimized the time the unit had to be down for final tie-ins. Instead of a wholesale replacement of the crude tower, overhead systems and heat exchanger train, engineers at Polaris added true value and found a solution which fit the client’s needs best.
Scope of Work
Process Engineering
Schedule
January 2006 – August 2008
Market
Refining
Location
South Central, TX